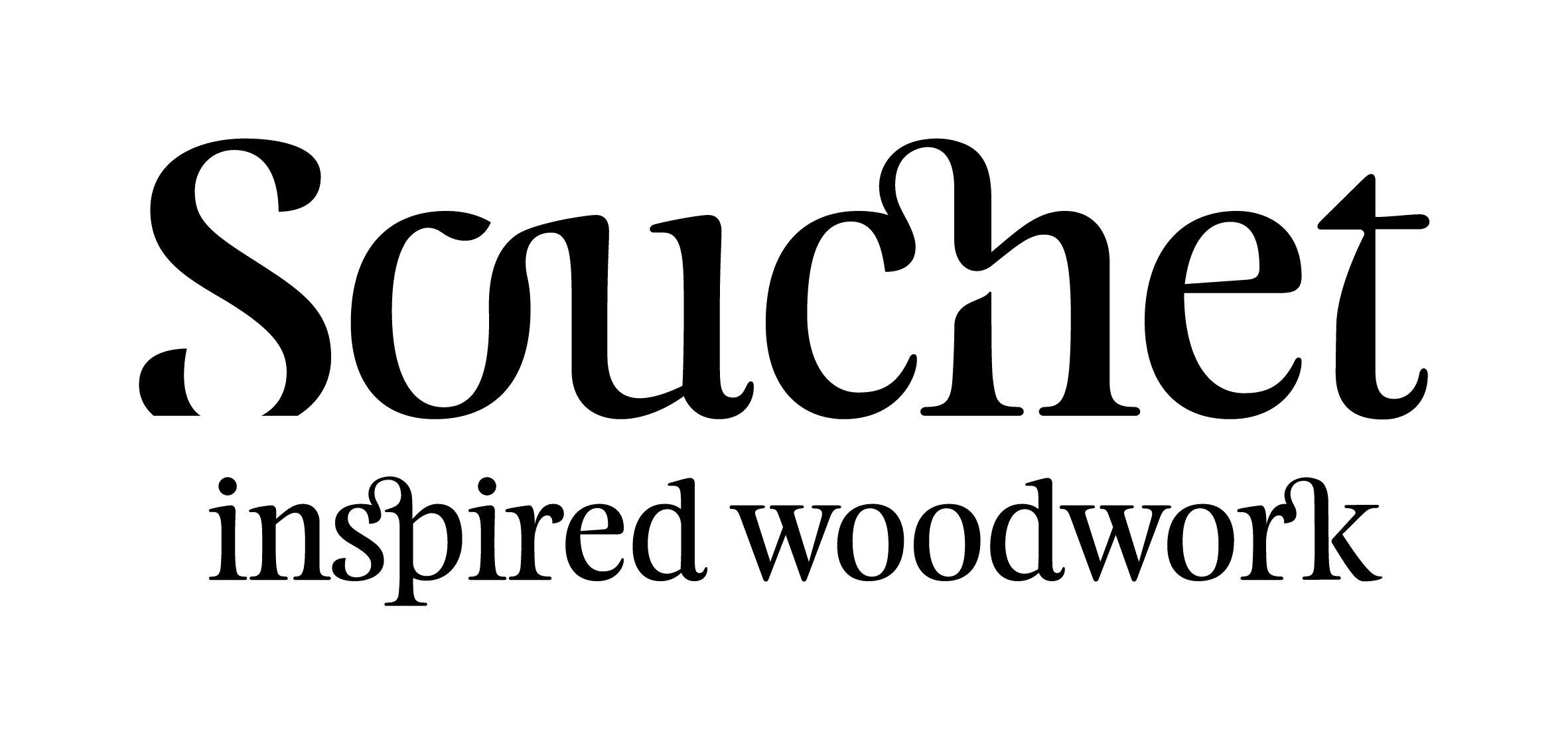
We are very happy to announce that Souchet Inspired Woodwork has joined the Par Excellence collective. This high-end woodworking workshop specializes in chair making and manufactures seats, sofas, coffee tables, side tables and consoles in their workshop in the French countryside. They work at the highest levels of craftsmanship and know-how and by working with the top gilders, carvers and upholsterers around France they make every project the best of the best. We sat down with the founder, Nicolas Souchet, to find out how they work in both traditional and contemporary methods to create such exceptional pieces.
Nicolas Souchet
We are so happy that you have joined Par Excellence. What are your thoughts on being part of this French design collective and what does it mean to Souchet Inspired Woodwork?
For the past ten years I have been working with Jouffre on projects where they would do the upholstery for my seating and we made wood structure for their seating. They introduced me to Par Excellence and I was immediately drawn to the fact that they work with artisans that have the highest expertise. They have the best straw marquetry artisans, the best decorative painters and so on. I believe strongly in being the best that you can be and working in the highest expertise and that we all have the same attention to details. When I work on projects with Jouffre, we come up with better solutions when we work together. There is a certain synergy that exists that makes one be the best that they can be. I am also very much looking forward to showing my brand in the US and I hope I can work on creating pieces with other Par Excellence artisans such as Atelier de Ricou and Atelier Saint-Jacques.
How did you become interested in woodworking, especially in chair making?
My father was a carpenter and when I was 15, he took me with him to visit the École Boulle, the famous school in Paris that opened in 1886 and trains students in the best of traditional arts and crafts. The school has different specialties such as upholsterer, finisher, metal worker and cabinetmaker, but when I walked into the chairmaker section, I said to my father right away that this was what I wanted to do for the rest of my life. 25 years later, I am still as passionate about chair making as I was when I was a teenager. During my 5 years at the École Boulle, besides chair making, I also learned upholstery, carving, gilding and wood turning. When working on projects today I know exactly what needs to be done when gilding and carving are required. I make the chair structure at my workshop, and I then work with a specialist in gilding etc. I am one of the best chair maker, so I want the best gilder, carver etc. I work with 3 gilders with one being a MOF (Meilleur Ouvrier de France – considered the best craftsmen of France). I also use 20 hand carvers that are located all around France.
Seats in the making, gilding and carving at the workshop
Following on the footsteps of your traditional skills your workshop has created digital and manufacturing processes that allow you to respond to unique requests. Can you please tell us about a project where you incorporated digital technology into your traditional woodworking process.
We recently completed a big project for a king. He wanted 10 chairs in the same design as a chair at the Louvre. They wanted the best details in the chairs so they came to us to recreate them. To hand carve these 10 chairs would take at least one year. I designed a machine where I can scan an object and the machine can do the first carving steps. The hand carver then finishes it by hand. Each chair has a slight variation as there is the “hand of that particular carver”. He adds his touch to the final product so that even though there were 10 chairs they are not exactly the same as if they had been made entirely by a machine. They have the spirit of the carver imbued in them.
With this scanning technology it saves us time for the initial manpower needed. For a new project for example, we create a sample of the chair’s leg which is hand carved. We then scan that and create a sample by machine that is then finished by the hand carver. Our attention to detail is meticulous and precise. We want to deliver the best. By saving time with using this machine we are able to provide good lead times for our clients.
CNC Machines
Please tell us a bit more about your workshop.
We have 20 craftsmen working at our workshop including several apprentices as we believe it is vital to train the next generation. My wife also works with me. She was an upholsterer and we met when we were both training at the École Boulle. She is now the artistic director at the workshop while I oversee the management of the company. I have been a chair maker for over 20 years and I still love my job. I have also found out that I love the management side of the work too. Having great working conditions, happy craftsmen, an efficient work flow it feels like being a conductor for an orchestra and it makes me so happy to see everything come together in a wonderful way.
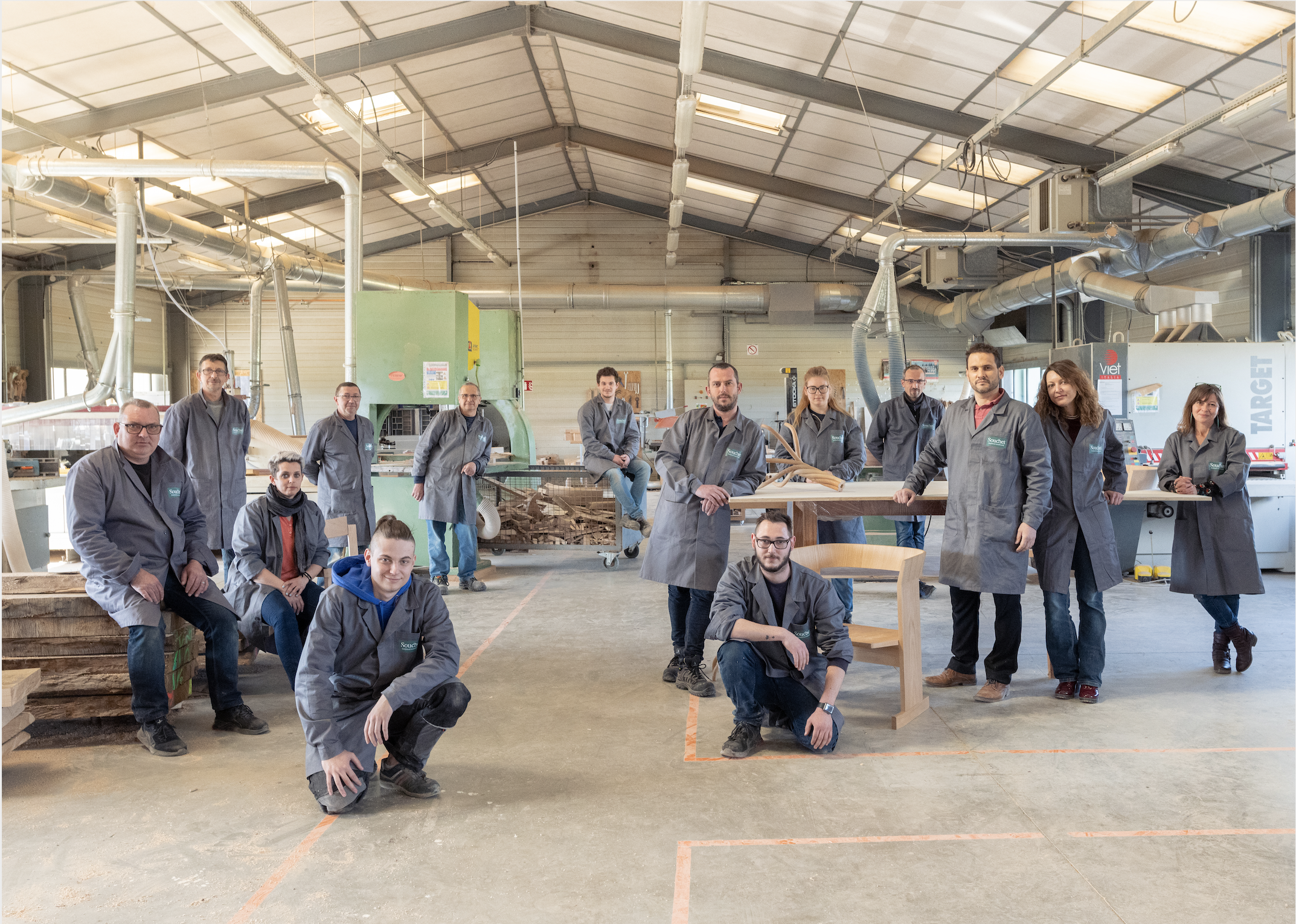
You have worked with so many outstanding designers. Do you have any dream projects?
Yes, I am so fortunate to work with so many wonderful designers such as Jacques Garcia and on special projects for Christian Liaigre. We have also worked with the yacht designers, Winch Design. We have done custom pieces for hotels and luxury residences. Our projects have taken us from London, Monaco, Switzerland, Australia, to Kiev and Moscow. I don’t have a dream project as I know how lucky I am to work on each project. I give the best of myself for each project and that always makes me happy.
Your workshop is exceptional in that you create both Traditional and Contemporary pieces at the highest level.
At the workshop we work both in Traditional and Contemporary styles. We have a solid base in Traditional woodworking with over 20 years of experience. I like working on Traditional pieces as I am always discovering new things, new forms, new assembly techniques while looking at historical pieces. I am always impressed and inspired by the 18th century designers as they worked with very simple tools and were very imaginative in the way they made new pieces for royalty. The 20th century was wonderful too as the best designers had an academic base.
For our contemporary pieces we use the experience of the traditional work and know-how and adapt it to a contemporary feel. It is very freeing with these designs as we are always searching for new materials and new processes on the machines.
Left photo shows a Traditional design; 3 contemporary pieces designed by Grégory Lacoua © Mario Simon-Lafleur
Please tell us about your new contemporary collection, “Lifflow”.
Interior designers know us for our traditional competency and our mastery of carpentry in seats but they didn’t know that we can do contemporary pieces. I worked on a yacht, created modern chairs for luxury apartments and villas but they were always confidential projects so I couldn’t include them in my portfolio. So, 2 years ago I began to create a collection called “Lifflow”. The name is a contraction of the name of the village where our workshop is located in France, Liffol-Le-Petit, and the word “flow” which indicates that we are moving into the future with movement and momentum. With our first collection we wanted to show our know-how, how we can make contemporary pieces simple but with complex detail. We are combining traditional know-how and innovative production techniques. This collection consists of 3 pieces featuring elegant lines in a resolutely contemporary spirit. The “Imperial” chair is influenced by Asian designs and lends an air of elegance and finesse in a simple but sculptural way. The curved top of the chair is very hard to do with machinery and this design emphasizes the raw materiality of wood in its simplest form. The “Love Blocks” chair is a lounge chair that showcases an ultra-minimalist style. I wanted it to feel like a stone, so it has a mineral aspect to it that also gives it a brutalist feel. We used a Kvadrat fabric designed by the former designer at Dior, Raf Simons and it was upholstered by Jouffre. There is a trompe l’oeil effect seen in the two blocks that seem to be unrelated and the seat is detached from the backrest. The “Twirl” side table has 6 pieces that twist and turn into a playful and organic form. It took 2 hours by machine and 20 hours by hand to create this exceptional detail. The interlacing of the base which is actually very light as it is entirely hollow shows a flexibility that seems unexpected for such a material as wood. It truly highlights the complexity and beauty of the exceptional craftsmanship at Souchet Inspired Woodwork. I wanted this collection to be very detailed oriented and precise while at the same time preserving the exceptional French know-how through the exploration of new technologies. It is a beautiful link between past and present. We also use local wood such as beech, oak and chestnut. The region where we are located has since the 17th century been a historic center of the manufacture of carpentry in seats and we are proud to be carrying on this tradition. This collection was imagined by the designer Gregory Lacoua, a classmate from the École Boulle and recent prizewinner of the “Grand Prix de la création de la ville de Paris in Design”.
The Imperial Chair, The Love Blocks chair and the Twirl Side table – all part of the Lifflow collection designed by Grégory Lacoua
© Mario Simon-Lafleur
Souchet Inspired Woodwork is committed to the manufacture and creation of the highest quality furniture by preserving traditional techniques and know-how as well as projecting these traditional artistic values into the contemporary world. Click here to see their exquisite craftsmanship.